Solutions
Coating in practice
Tailored coating processes with versatile applications. Our 6 brands are used in a wide range of industries: Customers from all over Switzerland and Europe rely on our expertise and quality awareness. We are pleased to portray some of them on this page.
Testimonials
P. Loher AG,
Zuzwil
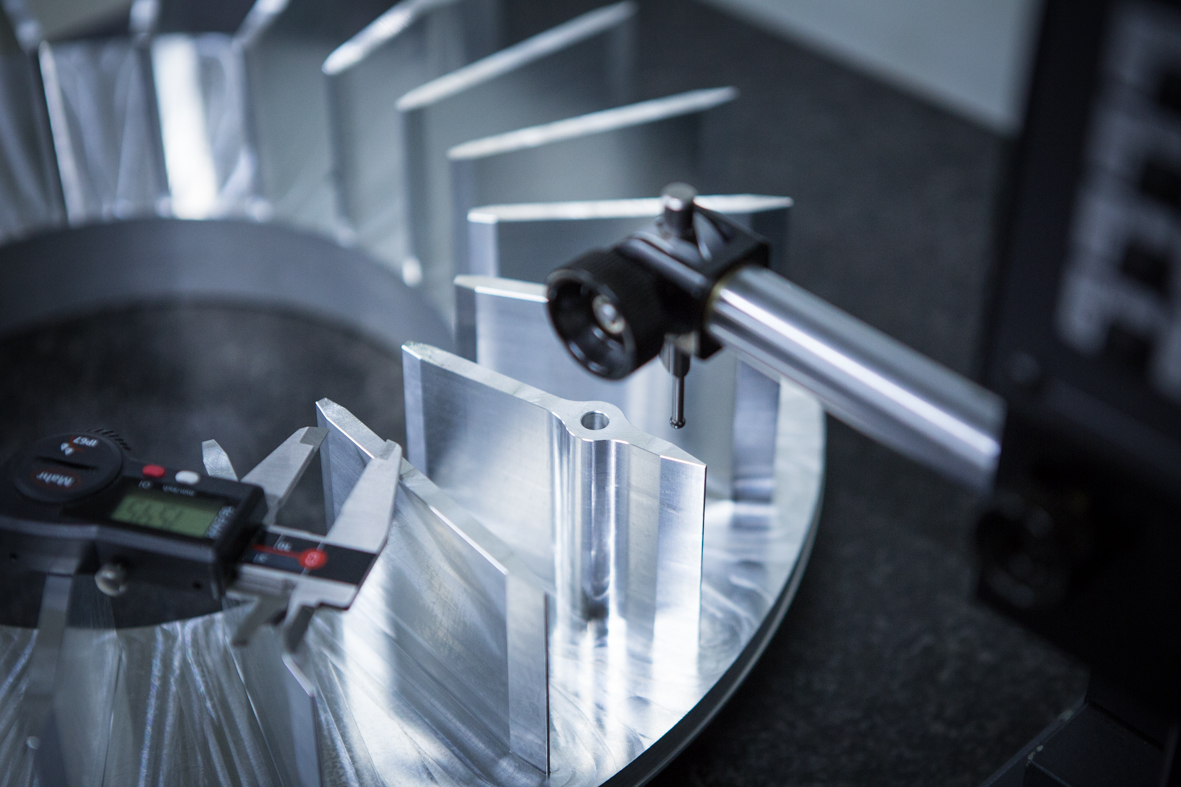
“You can tell that Altefco’s quality is top-notch as soon as you step into their production hall. Everything is orderly and clean. It perfectly reflects the final product. It is also important for us that we can call Altefco at any time. We receive prompt and straightforward assistance, and the service is always courteous and efficient. We couldn’t ask for anything better.”
Moreno Lamonato
Technical Officer
P. Loher AG
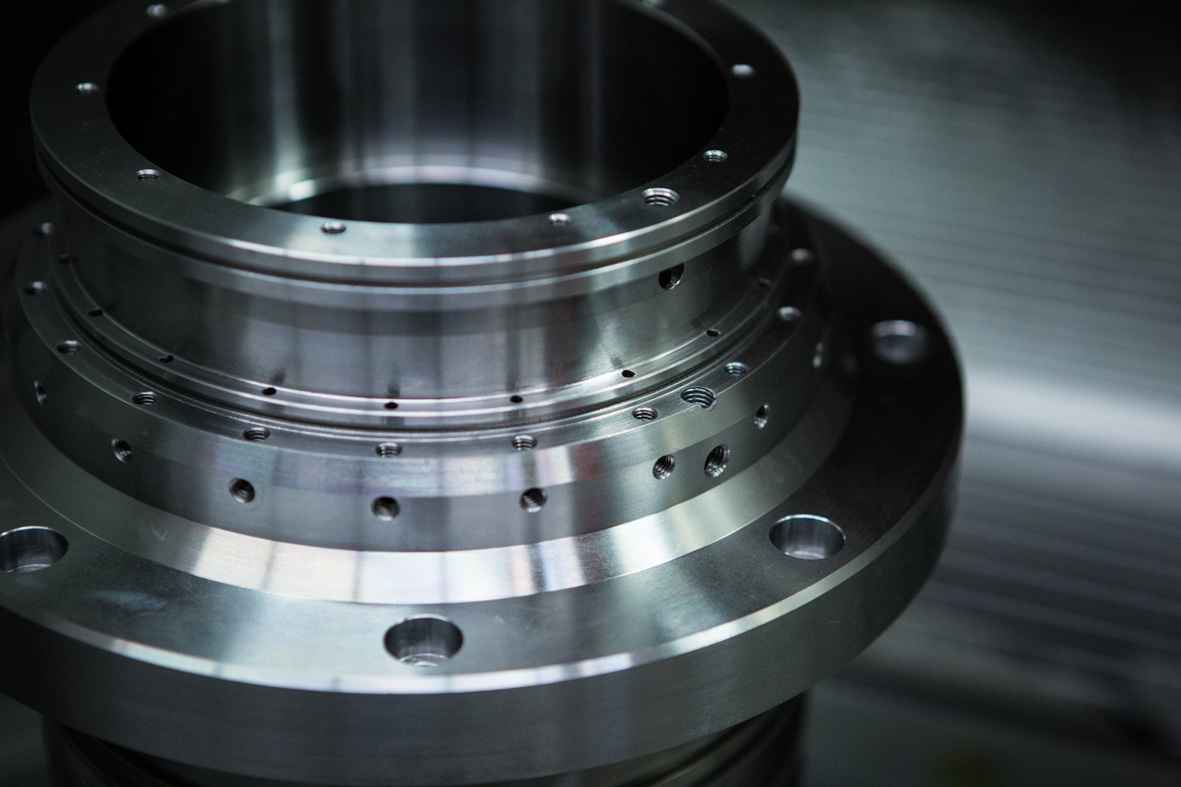
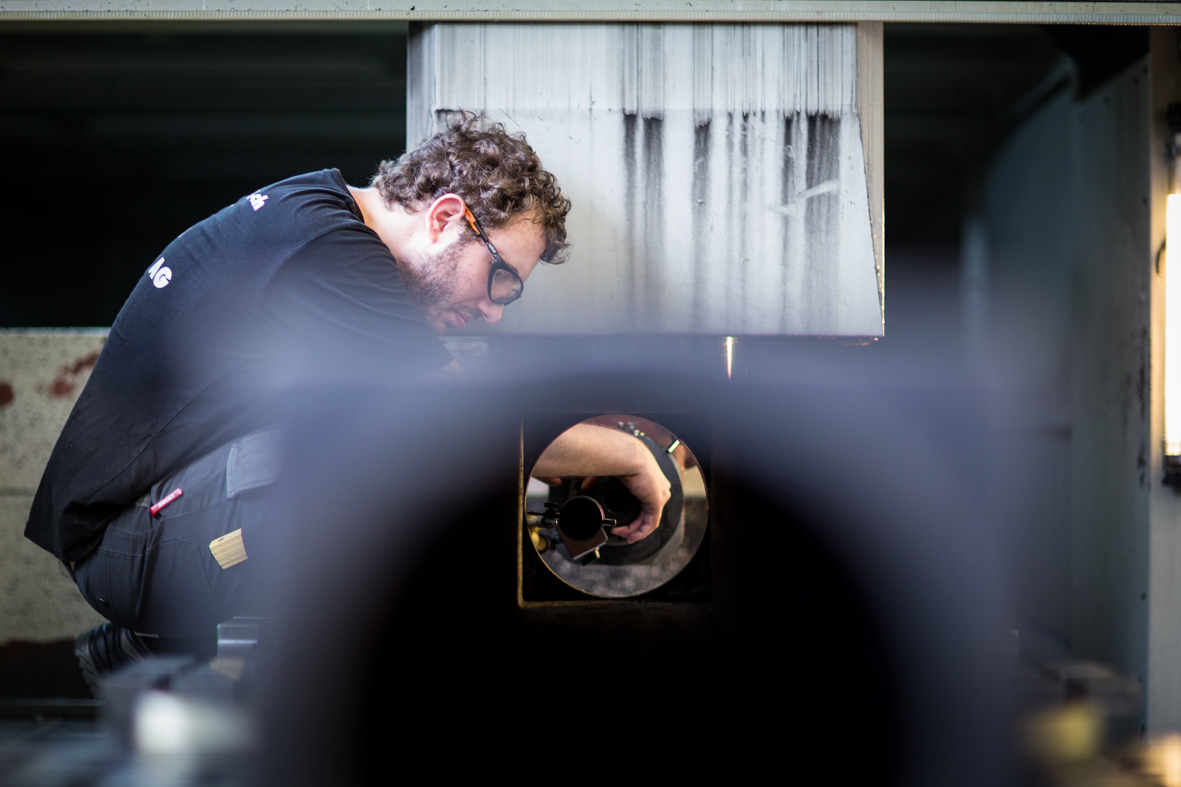
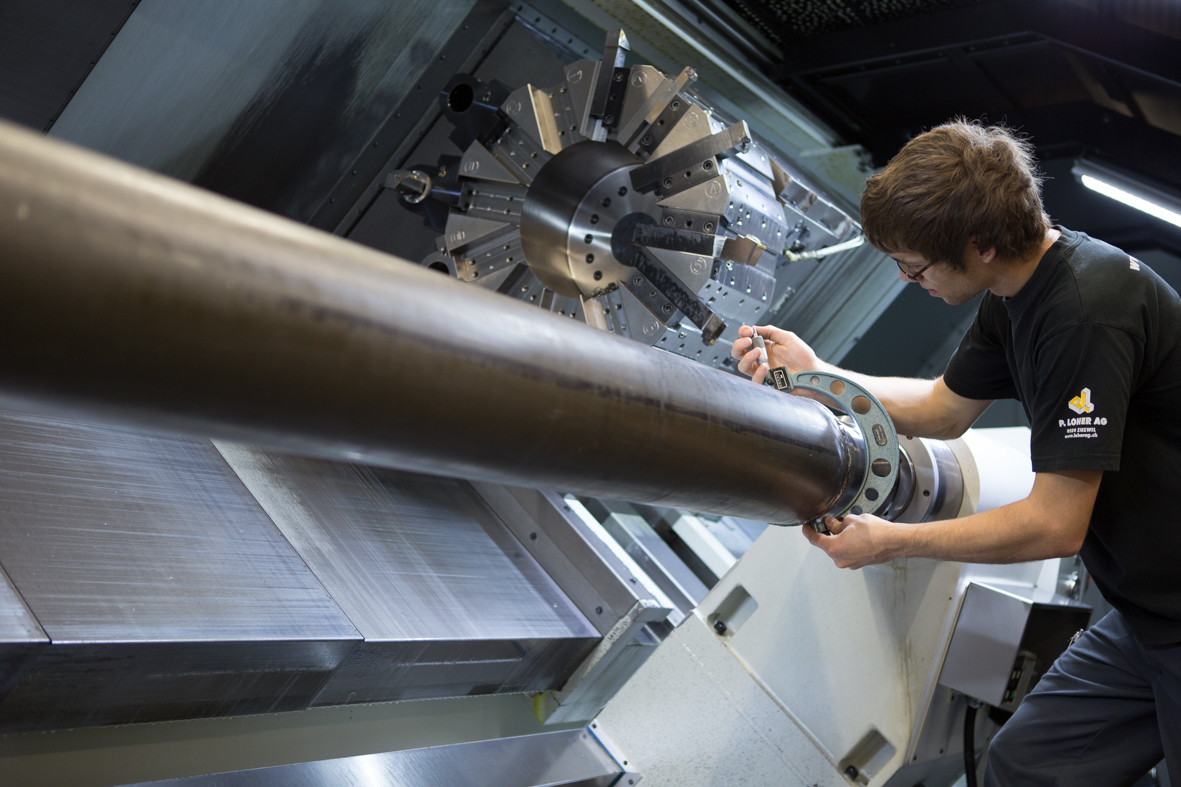
Photos: P. Loher AG
Service at the highest level
P. Loher AG
CNC turning and milling are the specialties of P. Loher AG, a trusted supplier to the machine industry. This SME, with 20 employees, manufactures both small and large parts, from prototypes to full production runs. Additionally, it offers surface treatment through reliable third-party providers. The company particularly values the helpful service it receives from Altefco.
Their CNC machines are operated on a piecework basis. The company has a strong reputation as a reliable contract manufacturer of milled and turned parts, working with a variety of materials including steel, non-ferrous metals and plastic. Meeting deadlines and maintaining quality standards are paramount for the company. “We shape the components and also take care of the final machining according to the drawing,” explains Moreno Lamonato, Technical Officer at P. Loher AG.
Customised Production
Precision is crucial in this context. This is particularly the case when surface treatment of the finished components is required. “We have to consider the coating from the very beginning, even if it’s just a matter of micrometres,” says the Technical Officer. P. Loher AG also works together with Altefco in the field of aluminium surface technology. “You can tell that Altefco’s quality is top-notch as soon as you step into their production hall. Everything is orderly and clean. It perfectly reflects the final product.” Moreno Lamonato particularly values the quick processing of quotes at Altefco. And that the written offer already includes the correct data for the preparation and delivery of the components.
Long-standing Partnership
The two SMEs from Eastern Switzerland have been working together for more than 20 years. A partnership that continually proves its worth, as Moreno Lamonato elaborates: “The regular collaboration creates a bond, and we know each other well. If we encounter issues, we can call Altefco any time. We receive prompt and straightforward assistance, and the service is always courteous and efficient. We couldn’t ask for anything better.”
Testimonials
EmbaPlan GmbH,
Walkringen
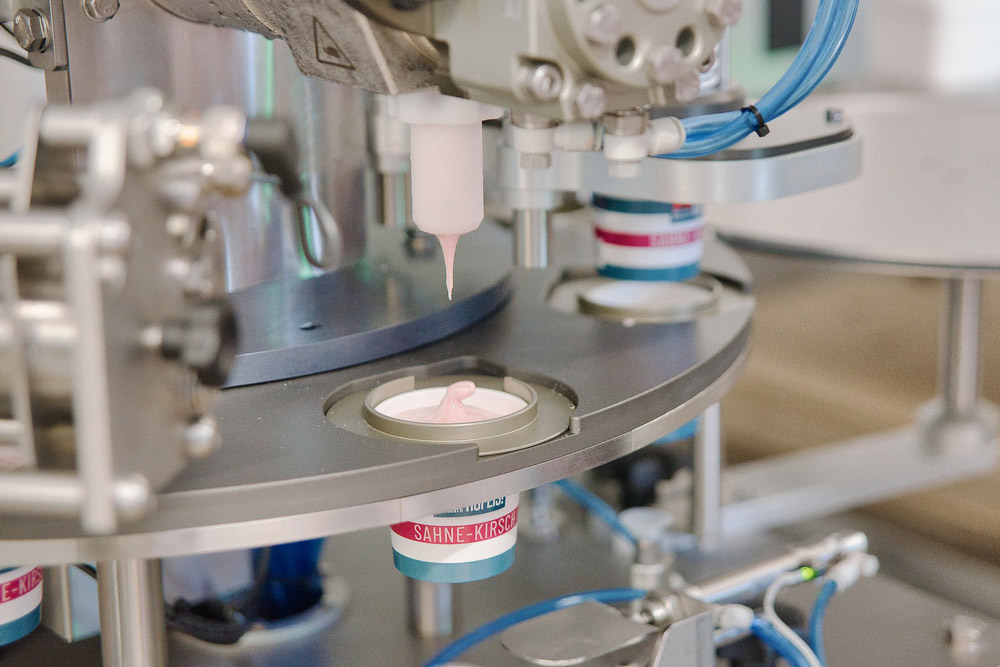
“We manufacture filling systems for the food industry, such as those used for yoghurt, ice cream, sauces, soups, beverages, and much more. We use parts made of aluminium, which are also hard Ematal coated by Altefco. We were impressed by the quality of the EMATEC® coating and the efficient working methods of Altefco from the outset. Their team always responds quickly and professionally, even in the most urgent cases when it comes to overhauls and repairs. We greatly appreciate that.”
Jonas Geissbühler
Head of Technology
EmbaPlan GmbH
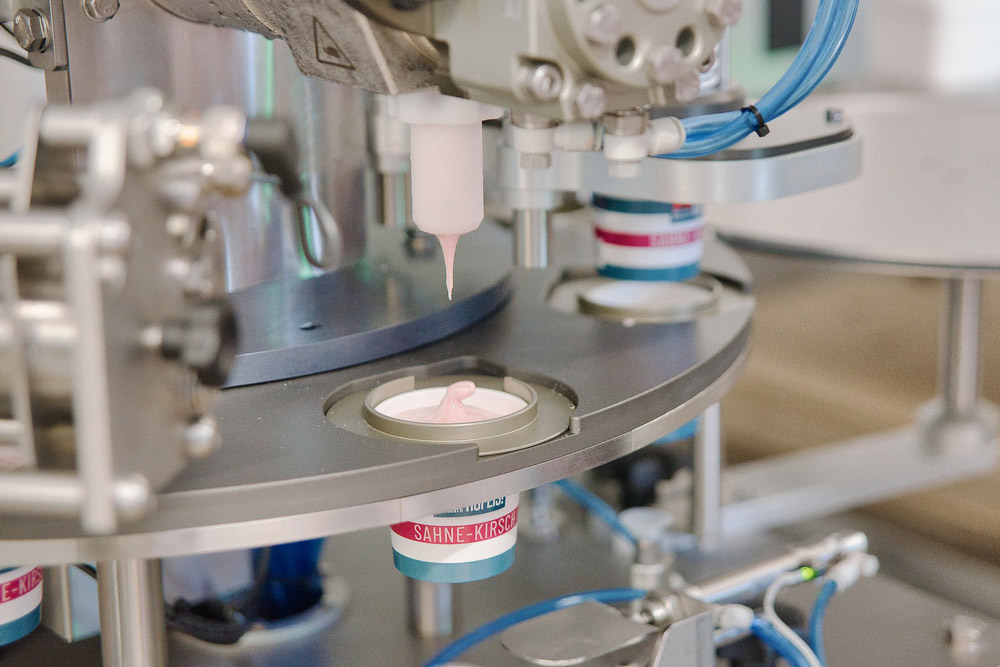
Foto: zVg EmbaPlan GmbH
Smart filling
EmbaPlan GmbH
EmbaPlan GmbH, based in Walkringen Bern, Switzerland, has teamed up with Altefco to refine its filling and dosing systems for yoghurts, ice creams and drinks. The EmbaPlan GmbH product range includes standard machines as well as tailor-made products to meet customer requirements. Aluminium components coated with EMATEC® are frequently used for this application.
When we open a yoghurt or ice cream cup, we rarely consider the process involved in producing this delightful dessert. Efficiently dosing and filling these types of food and drinks requires a surprising amount of effort. This is precisely where EmbaPlan GmbH, based in Walkringen, comes in. The company specialises in the manufacture of this type of filling systems and offers tailor-made machines as well as standard solutions.
Greater resistance to cleaning agents
The majority of the systems designed by EmbaPlan GmbH are made of stainless steel. Since this material is very heavy, lighter aluminium is used in certain parts of the system. “To make these parts more resistant, for example to cleaning agents, they need to be coated,” explains Jonas Geissbühler, who is responsible for development at EmbaPlan GmbH. Internal tests have shown that the hard Ematal coating technique is particularly suitable for this application. Embaplan GmbH has finally found the ideal partner for this stage of the project in Altefco.
Unrivalled delivery speed
Since the beginning of the partnership in spring 2023, Altefco has coated more than 300 machine parts for EmbaPlan GmbH, increasing their resistance. Jonas Geissbühler explains that the customer from the canton of Bern is extremely pleased with the outcomes. “Only a select few suppliers offer a solution similar to Altefco’s EMATEC® ‚” he explains. “We opted for Altefco because their fast delivery times of less than two weeks are unrivalled.” This is particularly important for urgent orders involving overhauls and repairs. The price/performance ratio offered by Altefco is also excellent, says the expert.
A carousel in the post
One of EmbaPlan GmbH’s classic products is the carousel, a turntable for filling yoghurt cups. The carousel is the largest component sent by post from Walkringen to Altefco in Thurgau. Jonas Geissbühler states that the carousel has a diameter of 70 centimetres and weighs approximately 4 kilograms. Other than that, EmbaPlan mainly sends smaller parts to Altefco. Another advantage of the low-porosity and titanium-containing EMATEC® aluminium oxide coating is that it is completely food-safe.
Testimonials
ProCNC AG,
Perlen
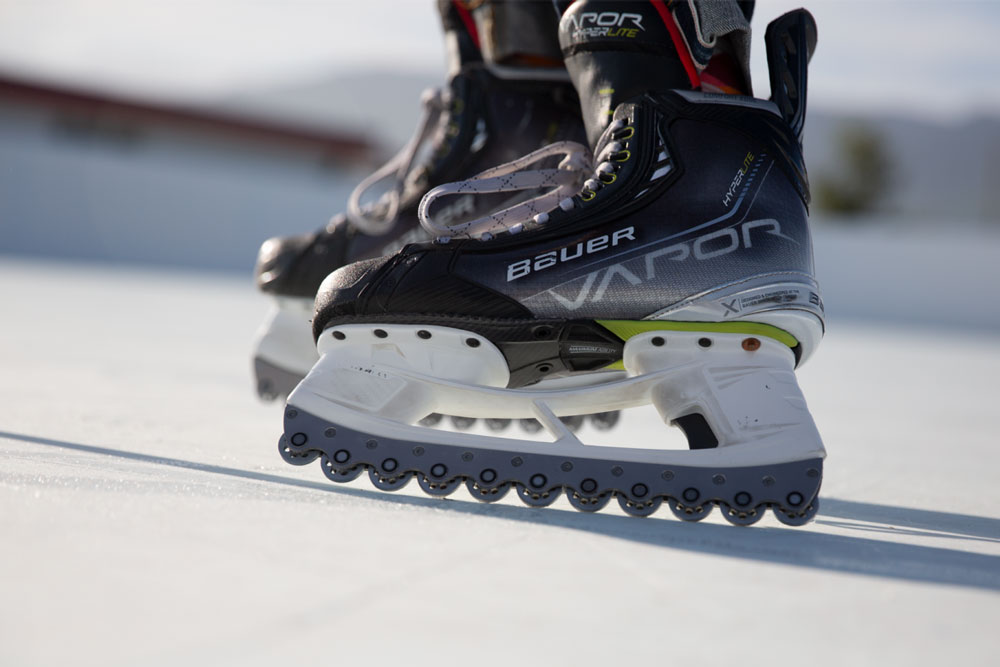
“As experts in CNC metal component production, we rely on dependable collaboration with our partners as we frequently need to respond promptly. For our new products, we need a partner that is prepared to work with us to develop a tailored solution that meets the customer’s needs. With Altefco, this works perfectly. They are flexible and can manufacture customised products. And the quality of their coatings is outstanding.”
Fabian Crusco
Head of AVOR
ProCNC AG
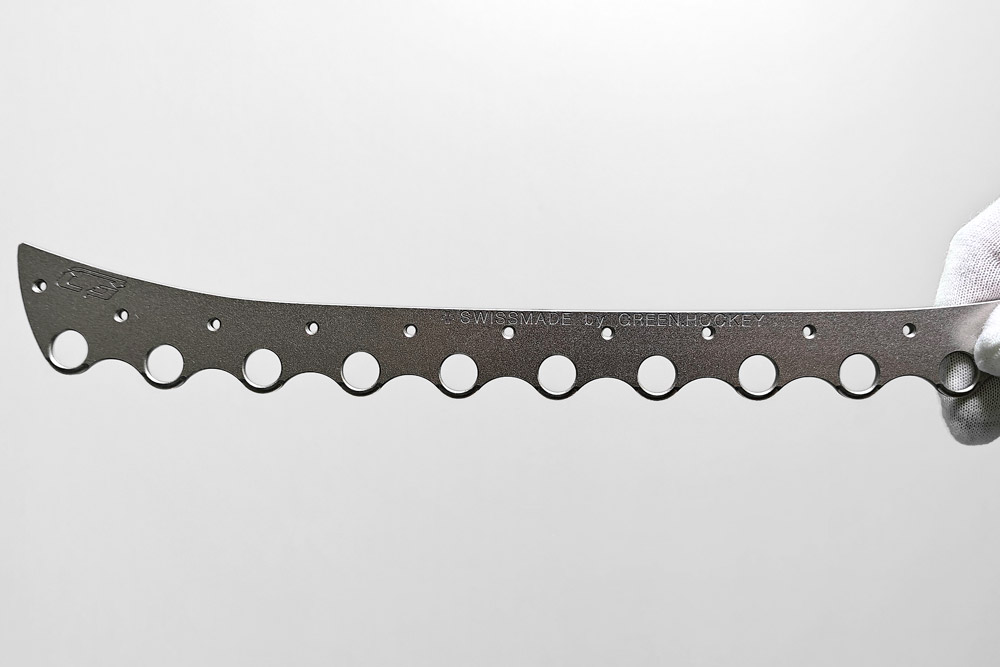
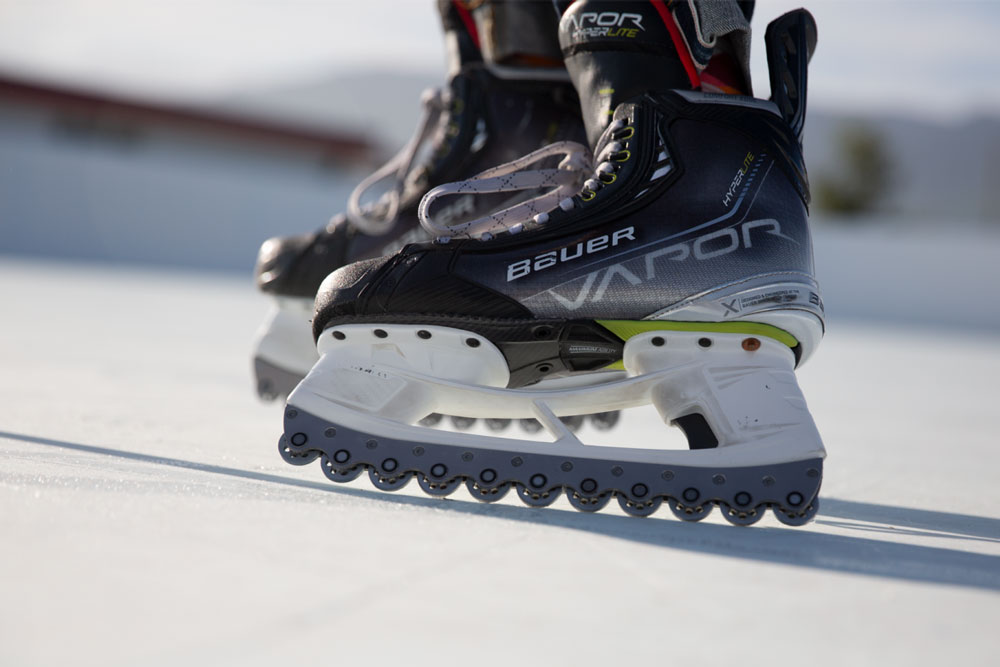
Tailor-made and hard-wearing
Hockey sideplates from ProCNC
How can ice hockey be made more sustainable? Riccardo Signorell, a former professional player, posed this question and, in collaboration with his business partner Dayana Signorell, founded the start-up Green Hockey. The two of them developed a new type of synthetic ice rink and the corresponding skate blades. The aluminium parts for the blades are manufactured by ProCNC, which in turn has them coated by Altefco.
Why produce new synthetic materials when there are already existing ones? Green Hockey AG was determined to develop a new type of synthetic ice rink, OCEANICE®, using recycled plastic waste. However, it is not possible to skate on them with conventional skates, but rather on the specially developed SHARKBLADES®, whose blades are equipped with small, sharp rollers that do not require sharpening.
In addition to the actual shoe, the SHARKBLADES® consist of a large number of individual parts, each of which underwent several iterations before they were deemed suitable for play by the professionals who tested them. The designers were keen to ensure that the feeling of skating on the synthetic surface was as close as possible to that on real ice. “Our task was to produce the sideplates, which are the two outer components of the blades. It was important for Green Hockey to achieve the same effect on the synthetic ice rink as conventional skates do on the ice,” explains Fabian Crusco, Head of AVOR at ProCNC. “The feedback from several players was factored into production, and we tested what was possible in terms of production technology.”
The challenge of colour consistency
the sideplates of the SHARKBLADE® runners are made of a special aluminium. “The client wanted the metal to have a consistent colour.” In order to accomplish this, ProCNC made sure that the raw material was highly homogeneous. The second challenge was to find a type of coating that would not change the silver colour and still offer the required wear resistance.
“We had a lively and intensive dialogue with the Altefco team. We had already had very good experiences with them on previous projects,” says Fabian Crusco. “We then tested it until it was functioning correctly.” For this purpose, Altefco customised the ANOTEC® anodising process to meet customer requirements. “We were impressed by the quality of the coating we received from Altefco, and our collaboration with them was highly cooperative once again”, says Fabian Crusco.
ProCNC was able to deliver the first series production of around 2000 sideplates for the SHARKBLADE® runners in various sizes on schedule in February 2024. They are already being used in several countries, including Canada and the USA. SHARKBLADES® and OCEANICE® can now also be purchased directly from green.hockey.
Testimonials
Zubler Handling AG,
Uzwil

“Altefco is conveniently located near us, allowing us to deliver and pick up our machine parts for coating in a flexible manner. As a tailor-made machine manufacturer for the plastic industry, we often need to react quickly. When time is of the essence, we receive support from Altefco. They have our back and meet the deadlines. And – we have practically zero defects.”
Remo Müller
Head of Purchasing and Manufacturing
Zubler Handling AG



Efficient and highly precise
Tailor-made machines from Zubler Handling
The production systems in the plastics industry are highly automated. This extends far beyond the actual production of injection moulded parts. Post-production processing in particular is extremely complex. Zubler Handling AG from Uzwil SG is a specialist in manufacturing tailor-made machines and excels in this niche.
“Injection moulded parts are removed from the mould, measured, inspected, stacked, packaged and labelled on the tailor-made automation systems from Zubler Handling,” explains Remo Müller, Head of Purchasing and Manufacturing at Zubler Handling AG. Among the plastic products processed with the company’s machines are, for example, precision parts for medical technology, packaging for the food industry and much more.
The machines come into direct contact with the finished plastic parts and one of the challenges in post-processing is handling the parts, which are often only millimetres in size, without damaging them during mechanical conveying. Furthermore, plastic parts for laboratory technology are produced in cleanrooms, which requires additional requirements. Abrasion, for example on conveyor belts and gripper arms, must be avoided at all costs. Therefore, various parts that come into contact with the plastic parts require very good slip properties. “Everything must run cleanly and precisely,” explains Remo Müller.
High productivity required
Zubler Handling machine parts are coated with ALTEF® or EMATEF®, depending on the application and function of the component. EMATEF® is mainly used for parts where superior slip properties are required. It provides a low roughness value, eliminating the need for expensive finishing (polishing). “We have a long-standing collaboration with Altefco in this field and are very satisfied,” says Remo Müller. “As a tailor-made machine manufacturer, we often need to react quickly. When the pressure is on, Altefco is there to back us up. They are very reliable.”
The plastics industry is highly competitive and Zubler Handling operates internationally. The Uzwil-based company offers its customers a comprehensive service, from engineering through to commissioning, maintenance and repairs. “Efficiency and productivity in the manufacture of our machines is essential for us to remain competitive,” says Remo Müller. “Altefco also supports us on this front. The company meets deadlines and delivers the best quality. And we have virtually zero rejects from the coating process.”
Suter Industries,
Turbenthal
“Suter Industries supplies anti-hopping clutches to race teams, motorbike manufacturers and dealers worldwide. They are characterised by a high degree of hardness and bond strength – and they look beautiful. Altefco is a technical leader in aluminium coating and ANOTEC® meets our high requirements. We are particularly impressed by the dimensional accuracy, the consistently high quality and the elegant visual appearance of our finished clutches.”
Roger Sutter
Production Manager
Suter Industries



Elegant and safe
Motorbike clutches from Suter Industries
The company Suter Industries from Turbenthal ZH has been using ANOTEC® from Altefco for coating motorbike clutches for over 20 years. Their flagship product, the “SUTERCLUTCH”, is extremely popular with racers, motorbike manufacturers and motorbike enthusiasts alike owing to its sophisticated engineering.
People who ride motorbikes do so out of passion. They take special care of their own bike, because it should offer maximum safety on the road and also look great. Suter Industries, a vehicle supplier in the motorbike, bicycle and energy sectors, is a manufacturing company with 45 employees. The company’s best-known products are anti-hopping clutches for motorbikes, of which it produces several thousand per year. Suter Industries supplies racing teams, various motorbike manufacturers and end customers.
Longstanding collaboration
Suter Industries has relied on Altefco as a coating partner in this area for over 20 years. “Altefco is the technical leader when it comes to aluminium coatings,” sagt Roger Sutter, production manager at Suter Industries. The collaboration developed, however, also because of the geographical proximity: “For us, it is easy to deliver and collect the parts in nearby Thurgau.” Altefco is also unrivalled in terms of processing speed: “A job usually takes a week – if it’s urgent, Altefco can do it in two days.”
Consistent quality
Hardness and bonding strength are crucial for the coating of motorbike clutches. That is why Suter Industries has opted for hard anodising with ANOTEC®. The process involves applying a layer of aluminium oxide, which protects the clutch from wear and corrosion. The surface of the base material is transformed in the process. This means that half of the coat thickness ‘grows’ into the base material, so that a standard thickness of 40 µm (40/1000 millimetres) results in an application of 20 µm. “We are particularly convinced by the dimensional accuracy,” says Roger Sutter. “Altefco’s coatings are always exactly the same thickness. We can rely on that.”
There is another good reason why Suter Industries works almost exclusively with Altefco for its motorbike clutches: “Our customers want their motorbike to look great,” says Roger Sutter. “An elegant appearance is therefore particularly important to us. ANOTEC® enables us to achieve this as well.”
TRIKNO AG,
Felben-Wellhausen
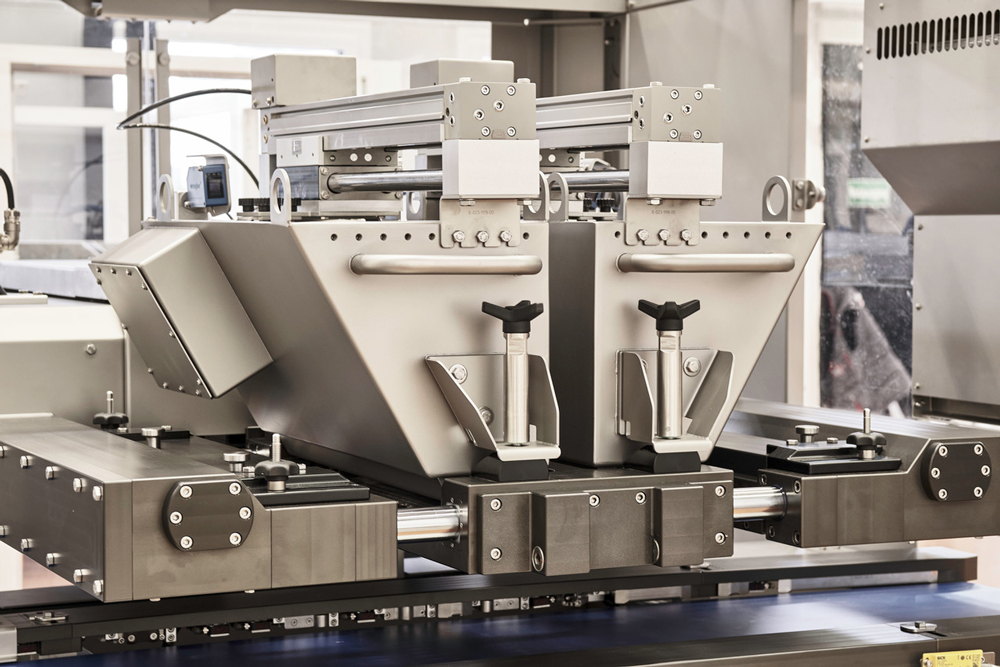
“We manufacture machinery for the chocolate industry. The core components of our systems are treated with an ALTEF® coating, which makes them harder and more scratch-resistant. Additionally, the surface gains better slip properties. Altefco provides exceptionally good consulting services. They help us whenever necessary and respond very quickly to inquiries. Adherence to delivery dates and consistent quality are further reasons why we have chosen Altefco.”
Joel Michel
Head of Purchasing
TRIKNO AG
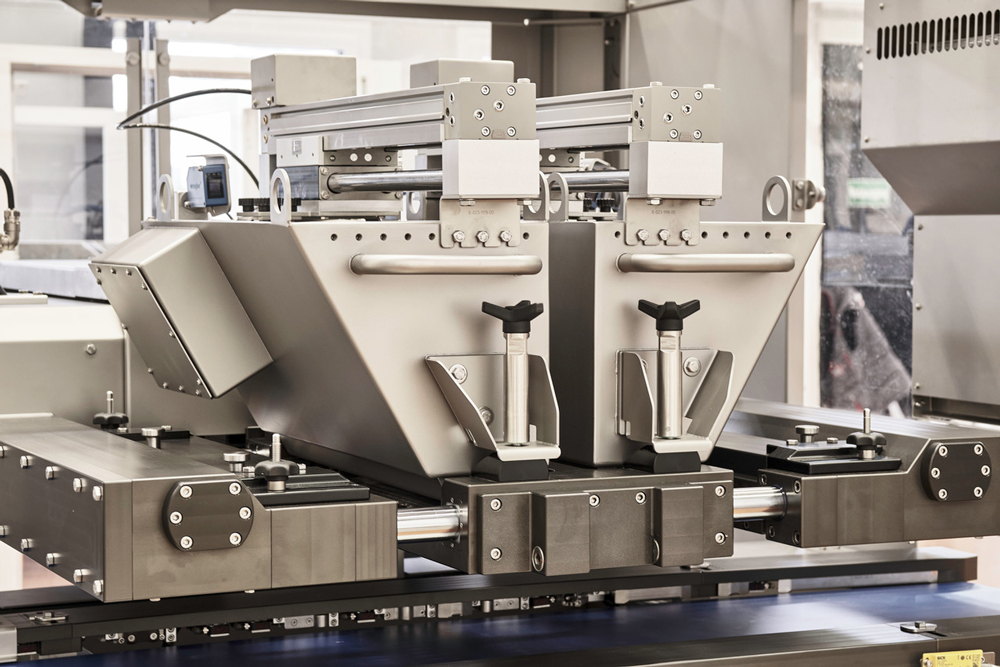
Robust and versatile
Chocolate production lines from TRIKNO AG
In chocolate production, versatility is the name of the game. TRIKNO AG from Felben-Wellhausen specialises in chocolate and confectionery machines and stands out for its customised solutions. The Thurgau-based company relies on Altefco for its aluminium coating.
The production of a praline is a highly complex matter. The initially liquid chocolate goes through a whole series of production steps on its way to becoming a finished confection. Starting with the production of the chocolate mass, to the moulding of hollow forms, to the brief stop on a vibration table for consistent shell thickness, to pouring in the filling, to preheating again under a bonnet, and finally to garnishing with nuts or other delicacies. TRIKNO AG specialises in such production lines and is represented with its equipment at almost all the major chocolate brands in Switzerland. “We cater to the individual needs of our customers and also offer prototype construction,” says Joël Michel, Head of Purchasing at TRIKNO AG.
Customer from the very beginning
For more than ten years, TRIKNO chocolate production line machine parts have been treated with aluminium coatings. “We have already had over 6800 parts coated at Altefco. We opt for ELOX and ALTEF® coatings,” says Joël Michel. The core parts of the production lines are coated with ALTEF® – this makes them harder and thus more scratch-resistant. It also increases the slip properties of the chocolate mass on the surface. External machine parts are given an ELOX coat – making them more corrosion-resistant and visually more appealing.
For the ultimate chocolate experience
It is particularly important for TRIKNO that both types of coating meet food safety standards: “We have to comply with many requirements in terms of food safety. The end product must not be contaminated. Altefco’s process puts us on the safe side,” explains the chocolate production expert. “Another advantage the coatings offer is extra protection when cleaning the machines.”
Machines are cleaned often, and when a product change is due, chocolate producers have to make sure that not even the smallest remnant of the previous product is left in the machine.
A partnership on equal terms
“Altefco’s aluminium coatings are not just surfaces, they bond with the material underneath and as a result are very durable,” says Joël Michel.
In addition to pralines, a wide variety of chocolate confections can be produced on TRIKNO lines – from simple chocolate bars to Easter bunnies and from chocolate bananas through to truffles or biscuit fillings. “Altefco has been familiar with our parts for a very long time and they have given us some good tips. We also get an immediate response when we have questions.”